One of the most important things IMARK members can do to add value for their customers is to understand recent changes to the National Electrical Code (NEC)—a regionally-adoptable standard for the safe installation of electrical wiring and equipment in the United Sates—and be able to explain how these changes may impact their contractor customers and ultimate end-users. IMARK Now invited industry experts from General Cable, Leviton, Legrand, Littelfuse and Thomas & Betts (a member of the ABB Group) to explain some of the most prominent changes made to the 2014 and 2017 NEC, and discuss why these changes can lead to positive commercial opportunities in 2017 and beyond.
Tamper-Resistance Receptacles—NEC Article 406.12
According to Legrand’s Steve Rood, tamper-resistant receptacles were first required in the 2008 NEC for residential applications in recognition of extensive data supporting numerous electrical injuries to children resulting from their insertion of conductive foreign objects into the openings of receptacles. Subsequently, to increase safety in other residential and commercial locations that are also often occupied by children and that present the same hazards for electrical burns and shock as receptacles in dwellings do, the NEC has consistently broadened corresponding installation requirements. As such, 2017 requirements for tamperresistant receptacles are now expanded to mobile homes, preschools and elementary education facilities, dormitories, corridors, business offices, outpatient facilities, auditoriums and numerous other “places of waiting” locations where small children are or can be likely to congregate.
Rood confirmed that several new application opportunities will be driven by this installation expansion of tamper-resistant receptacles. For dwelling units, receptacles installed in those locations specified by Sections 550.13 and 210.52 are now to be tamper-resistant. These sections address mobile and manufactured homes, as well as garages with more than one vehicle bay (where an additional receptacle per bay is now required). In addition, the areas and locations where tamper-resistant receptacles are now required as summarized in items four through seven of the expanded Section 406.12 are typically commercial-grade applications. Relative to wiring devices, these applications are normally characterized by product specifications at the project design stage for heavier-duty grade receptacles (often commonly referred to as “specification grade”), which tend to fetch higher unit sales prices than the residential versions. Increased business potential is expected over the next several years for significant upgrades, new additions or large renovations on scholastic, transportation and other similar public works projects where the growing demand for more power outlets will lead to increased electrical infrastructure opportunities. Additional quantities of new receptacles of all types and capabilities (GFCI, surge protection, isolated ground, USB charging receptacles, hospital grade and controlled outlets, as well as standard specification grade) will all need to be tamper-resistant wherever children can be expected to congregate in areas considered to be “places of waiting” or assembly. Anyone who has hunted in vain for an outlet at an airport, train station, hotel lobby or mall will eventually benefit from added installations of tamper-resistant receptacles to meet the market needs of more outlets that also simultaneously serve to increase safety.
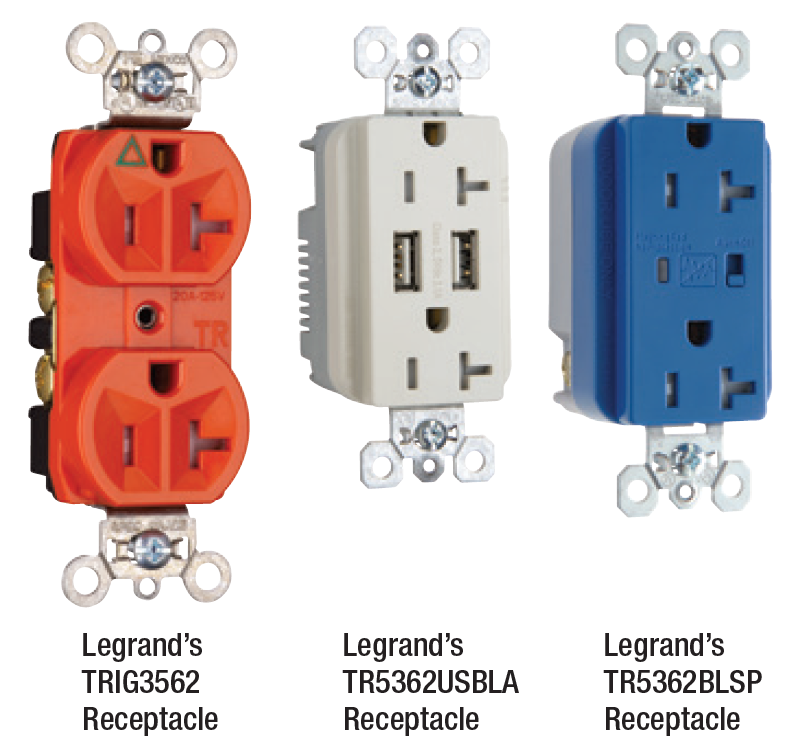
Meeting Rooms—NEC Section 210.71
According to Thomas & Betts’ David Kendall, this standard requires that each meeting room of not more than 93 square meters (1,000 square feet) in other than dwelling units must have outlets for non-locking-type, 125-volt, 15- or 20-ampere receptacles. Where a room or space is provided with movable partition(s), each room size shall be determined with the partition in the position that results in the smallest size meeting room. Meeting rooms are understood to be for gathering seated occupants where portable electronic equipment, such as computers or projectors, is likely to be used. Examples of rooms that are not meeting rooms include auditoriums, schoolrooms and coffee shops.
Receptacle outlets in fixed walls must be installed compliant with 210.52(A) (1) through (A)(4). A meeting room that is at least 3.7 meters (12 feet) wide and that has a floor area of at least 20 square meters (215 square feet) must have at least one receptacle outlet located in the floor at a distance not less than 1.8 meters (6 feet) from any fixed wall for each 20 square meters (215 square feet) or major portion of floor space. See Section 314.27(B) for floor boxes used for receptacles located in the floor.
The new NEC Section 210.71 requirement for meetings rooms was added to the 2017 NEC to address the lack of electrical receptacles available in a meeting room for use with computers, projectors, rechargeable phones and other electrical equipment or appliances. The total number of receptacle outlets installed in the fixed walls and floor will be determined by the dwelling requirements found in 210.52(A) per 201.71(B)(1) and (2). In addition, at least one floor box will be required for meeting rooms 215 square feet or larger.
Legrand’s Rood agreed, noting that another primary reason for this added section was to address and prevent potential trip and fall hazards created by cords being strewn across floors in meeting rooms. In addition, while many meeting rooms already had receptacles, they previously weren’t mandatory; as such, the 2017 NEC now ensures that meeting rooms will have them.
According to Legrand’s Rood, floor boxes and poke-thru solutions are currently popular with designers who want connections in the middle of rooms or underneath furniture rather than having people plug into walls (causing cables to be strewn about). In conjunction with and in addition to wall boxes, specifiers and building owners responsible for the design, layout and proper operation of meeting rooms will also find floor boxes and poke-thru devices to be helpful solutions when complying with Section 210.71 based on their enhanced flexibility, unobtrusiveness, availability in ADA-compliant versions and ability to meet challenging design criteria centered around on-grade/above-grade applications, fire classifications, multiple-gang capacities and plug load control for growing energy management requirements.
Arc Energy Reduction (Under Circuit Breakers)—NEC Article 240.87
According to Littelfuse’s Dave Scheuerman, this article was added in the 2014 edition of the NEC, though the true “effective” date varies depending on when your state (or local municipality) formally adopts the 2014 NEC. Article 240.87 was initially added in 2014 and expanded in the 2017 edition to provide methods for arc energy reduction when using circuit breakers with the underlying goal of reducing the clearing time at the available arcing current. Unless the circuit breaker’s clearing time is quicker than 0.07 seconds, one of the following methods must be used: zone-selective interlocking, differential relaying, energyreducing maintenance switching with local status indicator, energy-reducing active arc-flash mitigation system, an instantaneous trip-setting or an instantaneous override that’s less than the available arcing current or an approved equivalent means.
The arc-flash mitigation methods listed above offer a range of trip times, ease of selective coordination with the system and ease of retrofit within a user’s existing system. While various solutions can be used to help achieve each of the options involved, Littelfuse provides a family of products that can help achieve the shortest trip times of any methods listed. For example, arc-flash relays are high-speed arcdetection devices and Littelfuse offers three solutions that provide energyreducing, active arc-flash mitigation.
Expansion, Expansion-Deflection and Deflection Fittings—NEC Section 300.7(B)
Thomas & Betts’ Kendall said that this standard requires raceways to be provided with expansion, expansiondeflection or deflection fittings where necessary to compensate for thermal expansion, deflection and contraction.
According to Kendall, a standard expansion fitting works when the raceway is installed in a straight axial alignment, whereas the expansion/deflection fitting accommodates for the raceway’s thermal expansion or contraction when the raceway is offset or misaligned. Raceways are installed in an imperfect world and can be exposed to angular deflection due to the structure to which the raceway is mounted; expansion-deflection fittings can compensate for the angular deflection and thermal expansion and contraction of the raceway. The use of expansion-deflection fittings will prevent damage and separation of the raceway and maintain both mechanical and electrical continuity. The revised text makes it clear to inspectors, designers and contractors that expansion-deflection and deflection fittings are acceptable to be used with raceways to address thermal expansion, deflection and contraction.
To proactively address these changes, Thomas and Betts’ Fittings Non-Metallic Expansion/Deflection Coupling is UL approved, fully NEC 2014 compliant, safe and quick and easy to install, saving labor costs and minimizing the number of SKU parts needed.
Arc Energy Reduction (NEC Article 240.67)-- Under Cartridge Fuses and Fuseholders)
The 2017 edition of the NEC adds Article 240.67 with an effective date of Jan. 1, 2020 (again, pending formal adoption of this edition of the code per local state or other jurisdiction). In much the same way that Article 240.87 covers methods for arc energy reduction for circuit breakers, Littel-fuse’s Scheuerman said that Article 240.67 covers requirements for arc energy reduction for fuses and fusible switches rated 1,200 amperes or higher. This article states that unless the fuse’s clearing time is shorter than 0.07 seconds at the available arcing current, some other means of incident energy reduction should be utilized. The wording in Article 240.67 is very similar to the wording found in Article 240.87, with many of the same incident energy reduction methods included.
When talking about fuses rated greater than 1,200 amperes, the product solution quickly narrows to UL-listed Class L fuses, which are available in ratings as high as 6,000 amperes.
Expanded Applications for Surge Protection, Emergency Systems and COPS
Leviton’s Tom Degnan noted that past NEC code cycles expanded requirements relating to surge protection and that the 2017 NEC expanded these requirements even further, particularly as they relate to all emergency systems and critical operations power systems (COPS). Protecting these circuits from the damaging effects of surges is critical from a life-safety perspective.
Degnan said that COPS first appeared as new article 708 in the 2008 NEC, where it was inspired by the events of 9/11 and defined as “power systems for facilities or parts of facilities that require continuous operation for the reason of public safety, emergency management, national security or business continuity.”
According to Degnan, the following are several new 2017 NEC requirements relating to emergency systems and COPS:
- NEC Article 620.51(E) requires surge protection where any of the disconnecting means identified in 620.51 have been designated as supplying an emergency system load. Article 620.51 addresses elevators, escalators, dumbwaiters, moving walkways, platform lifts and stairway chairlifts. Essentially, if any of these devices are identified as being part of the facility’s emergency system or COPS, these devices must have a disconnect and the disconnect must be surge protected. Since the disconnect is surge protected, the elevator/escalator that’s controlled by the disconnect will effectively be surge protected as well.
- NEC Article 645.18 requires surge protection for critical operations data systems, equipment for public safety, emergency management, national security or business continuity. The intent is to keep these important lifesafety data systems operational by protecting them from surge spikes.
- NEC Article 695.15 requires surge protection for electric fire pump controllers. Motors that drive fire pumps must be protected so that they’re a reliable source of power.
- Finally (and though not technically part of emergency systems or COPS), NEC Article 670.6 requires surge protection for industrial machinery with safety interlock circuits, which protect workers and maintenance personnel.
There are many types of surge protective devices available to satisfy NEC requirements for surge protection.
Cable Ties Now Permitted for Securement and Support—NEC Sections 320.30(A), 330.30(A), 334.30(A), 348.30(A), 350.30(A), 356.30(1) and 362.30(A)
Kendall said that in general, the aforementioned sections were revised to permit cable ties to be used for “securement and support” of cables, flexible conduit and tubing, including cable ties that are listed to UL 62275 and identified as Type 2S or Type 21S, which are in accordance with the requirements at maximum spacing intervals specified in the code. Listing of cable ties approved for support of cables, flexible conduit and tubing are appropriate, as the standard requires markings that identify critical performance ranges that can affect their suitability for use, including minimum and maximum operating temperatures and resistance to ultraviolet light for outdoor installations. Cable ties identified as Type 1, Type 11, Type 2 or Type 21, without the “S” suffix for “securement and support,” are useful for wire management and supplemental means for routing conductors, flexible conduit or cable.
Rooftop Ampacities—NEC 310.15(B) (3)(c)
According to General Cable’s Sam Friedman, wiring installed on rooftops has been a topic of discussion and cause for changes to the NEC since the 2011 code. Because rooftop wiring is subject to higher temperatures due to increased sunlight exposure, Table 310.15(B)(3)(c) was included in the 2011 NEC to advise the required adjustment to ambient temperature when determining proper wire size to install on rooftops. This table required an adder to the ambient temperature depending on how high off the roof the wire was installed, with the adjustment amounting to as much as 33 degrees Celsius (60 degrees Fahrenheit) if the wire was placed 13 millimeters (1/2-inch) or less above the rooftop. Since this requirement could involve a significant increase in wire size, studies were conducted by General Cable and UL to determine if there were products that could handle the increased heat and, therefore, not require the de-rating. Testing showed that Type XHHW-2 cable was capable of withstanding a greater amount of heat than thermoplastic THHN product. As a result, an exception was included in the 2014 NEC to advise that XHHW-2 can be used without the need for any ambient adjustment factor. In the 2017 NEC, this section was again modified to change the requirement to indicate that no ambient adjustment is necessary if the wire is placed a minimum of 23 millimeters (7/8-inch) above the roof surface. If placed less than 23 millimeters (7/8-inch) from the roof surface, an adder of 33 degrees Celsius (60 degrees Fahrenheit) must be added to the outdoor temperature to determine ambient temperature for application of correction factors. However, the exception for XHHW-2 has remained.
Type SE for Temporary Power—NEC 590.4(B) and (C)
In the 2014 NEC, only NM and NM-C cables were permitted to be used in any “dwelling, building or structure without any height restriction or limitation by building construction type.” In the 2017 code, Type SE cables were included as a type of cable permitted for the same application as NM and NMC and for use as a temporary wiring method for branch circuits and feeders in raceways installed underground. This latter installation was necessary on construction sites where temporary power is run to job trailers and from building to building. In these applications, the use of overhead wiring isn’t practical due to cranes and heavy equipment. Type SE cable is manufactured and installed in accordance with Article 338 of the NEC. The 2017 edition has added Section 338.4, which requires that Type SE cables and associated fittings be listed.